A Comprehensive Look into NDT Chemicals: Preserving Aerospace Engineering's Future
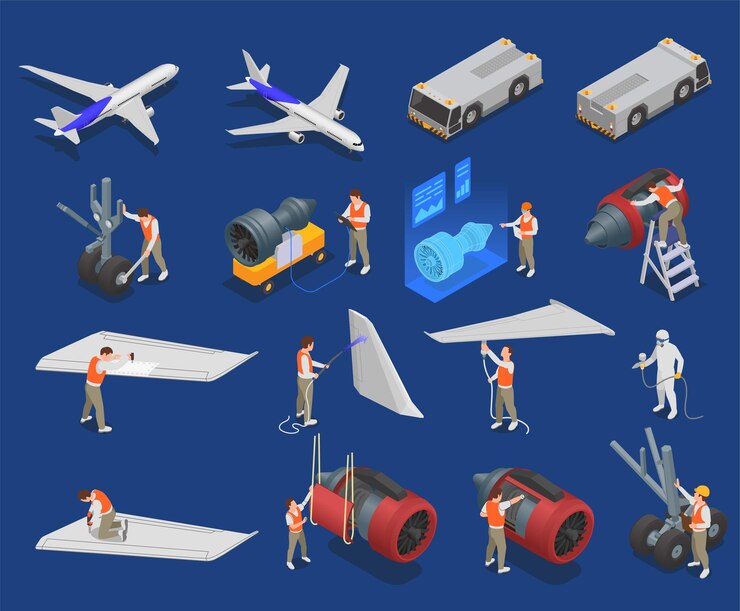
In aircraft engineering, where accuracy and safety are crucial, non-destructive testing, or NDT, is essential for guaranteeing the dependability of systems and componentry. Effective NDT is made possible in large part by NDT chemicals, which are specialised compounds used to find defects and abnormalities in materials without inflicting any harm.
Non-Destructive Testing (NDT): What is it?
NDT is a testing and analysis method that assesses a material's, component's, or system's qualities without making any permanent changes. In the aerospace industry, this technique is essential for locating flaws like as inclusions, voids, and fractures in structures ranging from fuselage panels to engine components.
Types of NDT Chemicals and How They Are Used
1. Chemicals Used in Penetrant Testing (PT) 1.
Liquid penetrant testing is among the most widely used NDT techniques. Applying a dye or fluorescent penetrant to a part's surface and letting it soak into any cracks or flaws is the method. A developer is used to extract the trapped liquid and expose defects once extra penetrant has been removed.
- Chemicals: developers, emulsifiers, cleansers, and penetrants
- Applications include identifying surface-breaking flaws in non-porous materials such as ceramics and metals.
2. Chemical Testing for Magnetic Particles (MT)
It is applied to ferromagnetic materials. The surface is sprayed with iron particles suspended in a liquid after a magnetic field is introduced. Discontinuities become apparent when the particles gather around them.
- Chemicals Used: Background contrast paints, carrier fluids, and dry or wet magnetic particles
- Applications: Finding defects on the surface and slightly below in steel parts such as landing gear and fasteners
3. Ultrasonic Couplant Testing (UT)
Ultrasonic testing looks for interior defects using high-frequency sound waves. Couplants are gels or liquids that let the test material and transducer communicate by transferring sound waves.
- Water-based or oil-based couplants are the chemicals used.
- Applications: Examining welds, composite materials, and constructions with thick walls
4. Radiographic Testing (RT) Developers
RT involves the use of X-rays or gamma rays. After exposure, radiographic films or digital detectors are developed using specific chemicals.
- Chemicals Used: Film developers, fixers, and rinsing agents
- Applications: Internal inspection of castings, welds, and complex assemblies
Benefits of Using NDT Chemicals in Aerospace
- Increased Safety: Early detection of defects helps prevent catastrophic failures.
- Cost Efficiency: Identifying flaws before they cause damage reduces repair and replacement costs.
- Compliance: Ensures adherence to strict aerospace industry standards.
- Extended Service Life: Enhances the reliability and longevity of critical components.
Environmental Aspects and Innovations
Environmental safety is being considered in the creation of modern NDT chemicals. Environmentally friendly formulas cut down on waste and toxicity. Digital integration and automation are also improving documentation and accuracy.
In conclusion
NDT chemicals play an increasingly important role as materials and aircraft systems become more complex and sophisticated. These materials are more than simply instruments; they are protections that guarantee the structural integrity of spaceships and aeroplanes. For aerospace engineering to have a safer and more dependable future, NDT technology and chemistry must continue to advance.